ОДНОПРИВОДНОЙ ВАЛОК ВЫСОКОГО ДАВЛЕНИЯ
Область применения
Одноприводные измельчающие валки высокого давления специально разработаны для предварительного измельчения цементного клинкера, минерального шлака, стального клинкера и т. д. в мелкие гранулы, а также для ультрадробления металлических минералов (железные руды, марганцевые руды, медные руды). , свинцово-цинковые руды, ванадиевые руды и др.) и для измельчения нерудных полезных ископаемых (угольных пород,
полевой шпат, нефелин, доломит, известняк, кварц и т. д.) в порошок.
Структура и принцип работы
◆Принципиальная схема работы
В шлифовальном валке высокого давления с одним приводом используется
Принцип измельчения экструзии агрегатов материала.
Один из них — стационарный, другой — подвижный.
Оба валка вращаются противоположно с одинаковой скоростью.
Материалы поступают через верхнее загрузочное отверстие,
и измельчаются за счет экструзии под высоким давлением в зазоре двух валков и выгружаются снизу.
◆Приводная часть
Нужен только один моторный привод,
мощность передается от неподвижного валка к подвижному через зубчатую систему,
так что два валка полностью синхронизированы без трения скольжения.
Вся работа используется для экструзии материала,
и коэффициент использования энергии высок, что экономит 45% электроэнергии по сравнению с обычными шлифовальными валками высокого давления.
◆Система приложения давления
Комбинированная пружинно-механическая система приложения давления позволяет подвижному ролику гибко уклоняться.
При попадании посторонних предметов из железа,
система приложения пружинного давления напрямую отступает и вовремя реагирует, обеспечивая эффективность работы до 95%;
в то время как традиционные шлифовальные валки высокого давления позволяют избежать этого, гидравлическое масло необходимо сливать через трубопровод для сброса давления.
Действие задерживается, что может привести к повреждению поверхности валка или неисправности гидравлической системы.
◆Поверхность рулона
Поверхность валка сварена из износостойкого сварочного материала, а твердость может достигать HRC58-65; давление автоматически регулируется вместе с материалом,
который не только достигает цели шлифования, но и защищает поверхность валка;
подвижный и неподвижный валки работают синхронно, без трения скольжения.
Таким образом, срок службы поверхности валка намного выше, чем у обычного шлифовального валка высокого давления.
Основные технические характеристики
◆ Высокая эффективность работы. По сравнению с традиционным дробильным оборудованием производительность переработки увеличивается на 40-50%.
Производительность обработки PGM1040 может достигать 50–100 т/ч при мощности всего 90 кВт.
◆ Низкое энергопотребление. В соответствии с способом привода с одним валком для привода требуется только один двигатель.
Потребление энергии очень низкое. По сравнению с традиционным HPGR с двойным приводом, он может снизить потребление энергии на 20–30%.
◆ Хорошее износостойкое качество. При работе только одного двигателя синхронизация двух валков очень хорошая.
Благодаря износостойким сварочным поверхностям валки обладают хорошей износостойкостью и легко обслуживаются.
◆ Высокая эффективность работы: ≥ 95%. Благодаря научному проектированию оборудование может находиться под давлением с помощью группы пружин высокого давления.
Рабочее давление можно регулировать автоматически в зависимости от сжатия пружинной группы. Точки неисправности нет.
◆ Высокая степень автоматизации и простота настройки. Без гидравлической системы вероятность возникновения неисправностей низкая.
◆ Поверхность валков сварена из износостойкого сварочного материала, обладающего высокой твердостью и хорошей износостойкостью;
Давление на пружину возникает за счет силы реакции материала, и давление всегда сбалансировано.
который не только достигает цели дробления,
но также защищает поверхность рулона; подвижный валок и неподвижный валок находятся в зацеплении и приводятся в движение системой зубчатых передач,
Скорость полностью синхронизирована, что позволяет избежать трения скольжения между материалом и поверхностью валка.
Поэтому срок службы намного выше, чем у двухприводного HPGR.
◆ Компактная конструкция и небольшая площадь.
Технические параметры
Модель | Диаметр рулонаmm | Рулонширина мм | Макс.размер подачи(Цемент, стальной шлак, рудный шлак) мм | Оптимальный кормразмер(металлическийМ И Н Е Р А Л ,неметаллическийминерал) мм | ммВыходной размер(цемент)мм | Производительность обработкиТ/ч | Мотормощность, кВт | Габаритные размеры(Д×Ш×В)mm |
PGM0850 | φ800 | 500 | 50 | 30 | Классификация,<4 | 30~40 | 37 | 2760×2465×1362 |
PGM1040 | φ1000 | 400 | 50 | 30 | Классификация,<4 | 50~80 | 90 | 4685×4300×2020 |
PGM1060 | φ1000 | 600 | 50 | 30 | Классификация,<4 | 70~110 | 110 | 4685×4300×2020 |
PGM1065 | φ1000 | 650 | 50 | 30 | классифицирующий,<4 | 100~160 | 200 | 5560×4500×2200 |
ПГМ1250 | φ1200 | 500 | 50 | 30 | Классификация,<4 | 120~180 | 250 | 6485×4700×2485 |
PGM1465 | φ1400 | 650 | 50 | 30 | Классификация,<4 | 240~320 | 630 | 9200×6320×3600 |
PGM1610 | φ1600 | 1000 | 50 | 30 | Классификация,<4 | 500~650 | 1250 | 10800×8100×4400 |
СРАВНЕНИЕ ОДНОПРИВОДНОГО ВДВД И ОБЫЧНОГО ВДВД
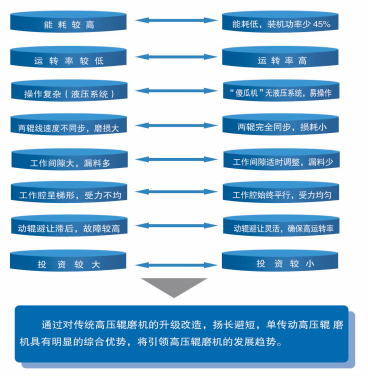
СХЕМА ПРОЦЕССА ПРЕДВАРИТЕЛЬНОГО ИЗМЕЛЬЧЕНИЯ ОДНОПРИВОДНОГО ВДВД
Предварительное измельчение цемента, рудного шлака и стального шлака «Больше дробления и меньше измельчения, замените измельчение дроблением», то есть предварительное измельчение, стало основной технологией производственного процесса трубопрокатных заводов для увеличения производительности и снижения энергопотребления. . Являясь самым современным энергосберегающим оборудованием для предварительного измельчения, HPGR с одним приводом может дробить материалы до -4 мм или -0,5 мм, из которых на 0,08 мм приходится более 30%. Производительность используемой шаровой мельницы можно увеличить на 50–100%, а энергопотребление системы измельчения можно снизить на 15–30%.
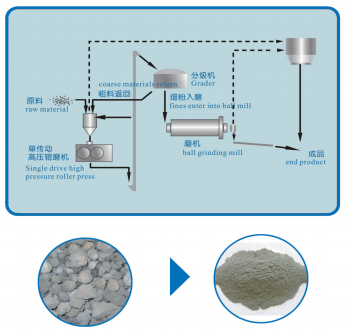
ТЕХНОЛОГИЧЕСКАЯ СХЕМА ПРОЦЕССА СВЕРХМЕЛКОГО ИЗМЕЛЬЧЕНИЯ МЕТАЛЛИЧЕСКОГО МИНЕРАЛА С ОДНОРОДНЫМ ПРИВОДОМ HPGR
Ультратонкое дробление металлических минералов
Когда минералы проходят через зазор между двумя валками, они измельчаются на мелкие частицы размером -5 мм или -3 мм и большое количество порошка под действием силы высокого давления. Из-за слабой силы связи между полезным минералом и пустой породой легко возникают усталостные разрушения или микротрещины и внутренние напряжения. Часть интерфейса будет полностью диссоциирована.
За счет высокого содержания мелкодисперсного порошка, выгружаемого из ВДГР, и того, что минералы измельчаются по поверхности диссоциации, по сравнению с традиционным дроблением снижается доля срастаний в измельченных продуктах и снижается выброс хвостов. эффект хороший.
Значительно улучшаются как качество грубого концентрата, так и выход отходов.
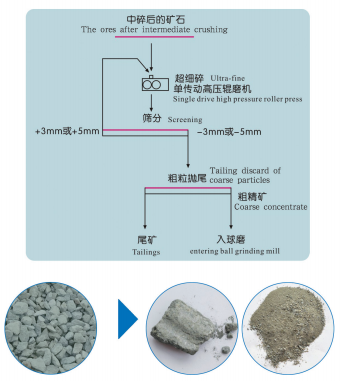
СХЕМА ПРОЦЕССА ПРИМЕНЕНИЯ НЕМЕТАЛЛИЧЕСКИХ МИНЕРАЛОВ С ОДНОРОДНЫМ ПРИВОДОМ HPGR
Измельчение неметаллических минералов
По сравнению с традиционным шлифовальным оборудованием, HPGR с одним приводом обладает преимуществами большой производительности одной машины, низкого энергопотребления, меньшего износа и меньшего загрязнения железом; Тонкость продукта можно контролировать от 20 до 120 меш, что может заменить шаровую мельницу и создать новый процесс измельчения.
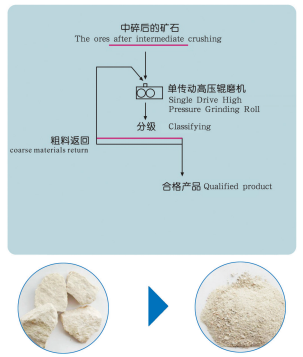
СЕРИЯ HPGM ШЛИФОВАЛЬНЫЕ ВАЛКИ ВЫСОКОГО ДАВЛЕНИЯ
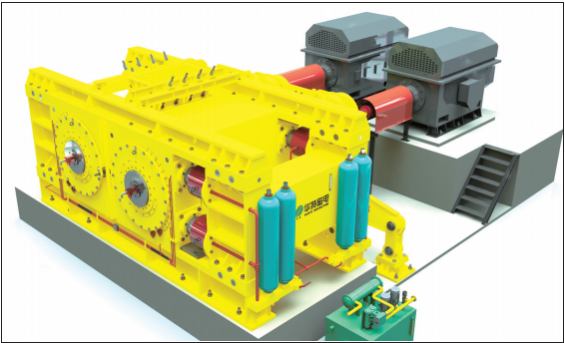
Принцип работы
Шлифовальные валки высокого давления серии HPGM — это новый тип энергосберегающего шлифовального оборудования, разработанный по принципу измельчения слоя материала под высоким давлением. Он состоит из двух отжимных валков, которые вращаются синхронно с небольшой скоростью. Один из них представляет собой неподвижный валок, а другой — подвижный валок, оба из которых приводятся в движение мощным двигателем. Материалы равномерно подаются сверху двух валков и непрерывно переносятся в зазор между валками прижимным валком. После воздействия высокого давления 50-300 МПа осадок плотного материала выгружается из машины. В кеке выгружаемого материала, помимо определенной доли квалифицированных продуктов, внутренняя структура частиц неквалифицированных продуктов заполнена большим количеством микротрещин из-за экструзии под высоким давлением, так что измельчаемость материала снижается. значительно улучшилось. Для материалов после экструзии, после дробления, классификации и сортировки, доля мелких материалов размером менее 0,8 мм может достигать около 30%, а материалов размером менее 5 мм — более 80%. Таким образом, в дальнейшем процессе измельчения потребление энергии измельчения может быть значительно снижено, так что производственная мощность измельчительного оборудования может быть полностью задействована, обычно производительность системы шаровой мельницы может быть увеличена на 20% ~ 50. %, а общее энергопотребление можно снизить на 30–50 % и более.
Области применения
В Китае имеется много видов ресурсов металлических руд, но качество большинства минеральных разновидностей плохое, разнородное и хорошее. В целях решения нерешенных проблем в экономическом, техническом и природоохранном аспектах развития горнодобывающей промышленности отечественные металлургические предприятия активно внедряют, осваивают и осваивают зарубежное новое и эффективное горнодобывающее производственное оборудование. На этом рынке HPGR представляет собой высокоэффективное шлифовальное оборудование, впервые исследованное и продемонстрированное, которое начинает использоваться на отечественных горнодобывающих предприятиях. Это также горнодобывающее оборудование, которое больше всего беспокоит отечественную горнодобывающую промышленность. Можно сказать, что HPGR широко используется на отечественных металлических рудниках. HPGR широко используется в стране и за рубежом для измельчения в цементной промышленности, грануляции в химической промышленности и тонкого измельчения окатышей для увеличения удельной поверхности. Он используется для дробления металлической руды для достижения различных целей, таких как упрощение процесса дробления, большее дробление и меньшее измельчение, повышение производительности системы, улучшение эффекта измельчения или показателей разделения.
Практическая область применения
1. Среднее, тонкое и сверхтонкое измельчение сыпучих материалов.
2. В горнодобывающей промышленности его можно разместить перед шаровой мельницей в качестве оборудования для предварительного измельчения или составить комбинированную систему измельчения с шаровой мельницей.
3. В промышленности по производству окисленных гранул можно заменить обычно используемую влажную мельницу.
4. В строительных материалах, огнеупорных материалах и других отраслях промышленности успешно применяются цементный клинкер, известняк, боксит и другие помолы.
Преимущества продукта
1. Конструкция с постоянным давлением обеспечивает плавное давление между валками и эффект дробления.
2. Автоматическая коррекция отклонений позволяет быстро регулировать зазор между валками, чтобы обеспечить плавность работы оборудования.
3. Система разделения кромок снижает влияние кромок на эффект дробления.
4. Со шпильками из цементированного карбида, длительным сроком службы, простотой обслуживания и возможностью замены.
5. Блок клапанов использует импортные компоненты, а гидравлическая система имеет разумную конструкцию и высокую надежность.
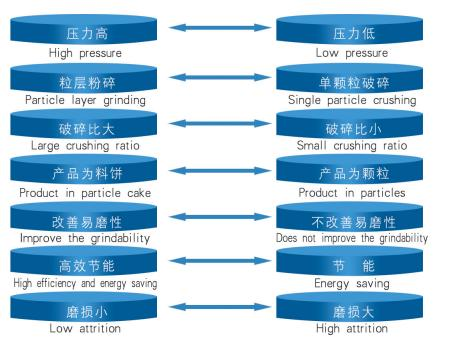
Структура ВДГР
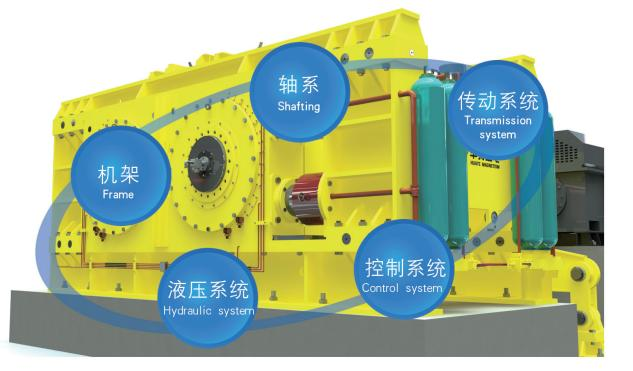
Модель | Диаметр рулонаmm | Ширина рулона мм | Пропускная способностьемкость | Размер подачи | Вес машиныt | Установленная мощность |
HPGM0630 | 600 | 300 | 25-40 | 10-30 | 6 | 74 |
HPGM0850 | 800 | 500 | 50-110 | 20-35 | 25 | 150-220 |
HPGM1050 | 1000 | 500 | 90-200 | 20-35 | 52 | 260-400 |
HPGM1250 | 1200 | 500 | 170-300 | 20-35 | 75 | 500-640 |
HPGM1260 | 1200 | 600 | 200-400 | 20-35 | 78 | 600-800 |
HPGM1450 | 1400 | 500 | 200-400 | 30-40 | 168 | 600-800 |
HPGM1480 | 1400 | 800 | 270-630 | 30-40 | 172 | 800-1260 |
HPGM16100 | 1600 | 1000 | 470-1000 | 30-50 | 220 | 14.00-20.00 |
HPGM16120 | 1600 | 1200 | 570-1120 | 30-50 | 230 | 16:00-22:40 |
HPGM16140 | 1600 | 1400 | 700-1250 | 30-50 | 240 | 2000-2500 |
HPGM18100 | 1800 г. | 1000 | 540-1120 | 30-60 | 225 | 16:00-22:40 |
HPGM18160 | 1800 г. | 1600 | 840-1600 | 30-60 | 320 | 2500-3200 |
Технология поверхности валков нового типа
Он использует высококачественные шпильки из твердого сплава с высокой твердостью и хорошей износостойкостью.
Расположение шпилек разработано с помощью компьютерного моделирования.
и разумное расположение, которое может образовывать однородный слой материала между шипами, эффективно защищая шипы и поверхности роликов,
и улучшение срока службы сжимающего вала. Шпильки устанавливаются с помощью импортного специального клея для облегчения замены.
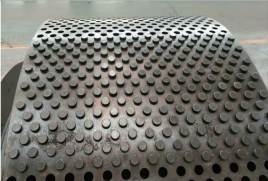
Технология разделения втулки ролика и главного вала
Основная часть прижимного вала изготовлена из высококачественной кованой стали, а втулка валка - из высококачественной легированной стали. Главный вал и валки изготовлены из разных материалов, что повышает прочность главного вала и жесткость втулки валка. Срок службы втулки вала значительно увеличивается. Замена втулки ролика удобна.
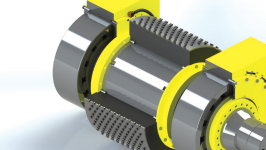
Технология быстрого монтажа и демонтажа подшипников. Используются высококачественные подшипники с коническими отверстиями и предварительно отформованный масляный бак высокого давления. Подшипник можно легко демонтировать с помощью масляного насоса высокого давления, что значительно снижает сложность замены подшипника и повышает эффективность технического обслуживания.
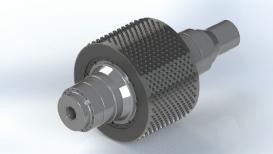
Технология множественного комбинированного уплотнения
В уплотнении подшипника используются различные уплотнения J-типа, V-образного типа и лабиринтные уплотнения, а комбинированная технология уплотнения эффективно обеспечивает уплотняющий эффект подшипника.
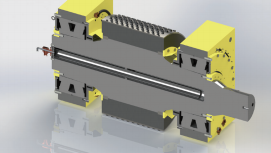
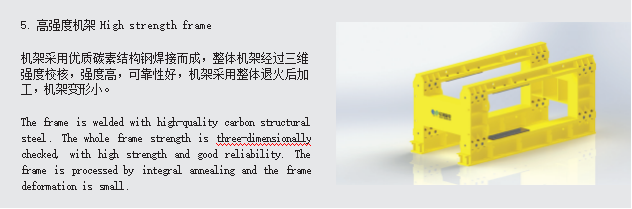
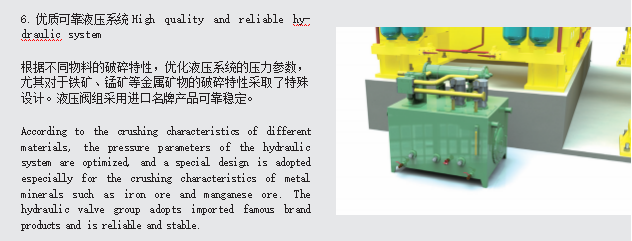
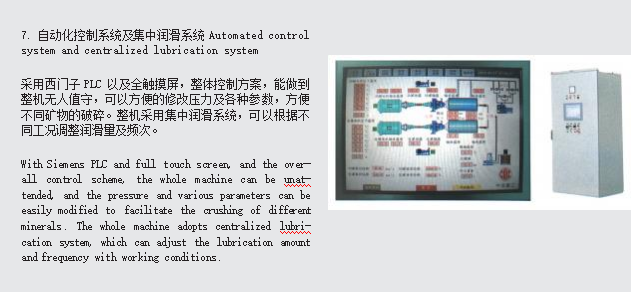
Поток обогащения железной руды
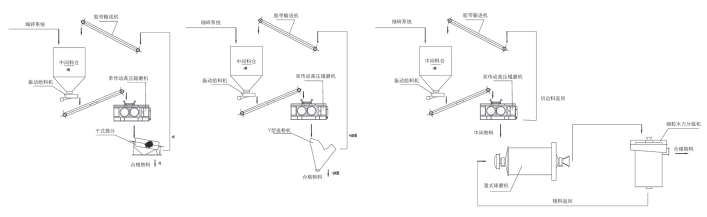
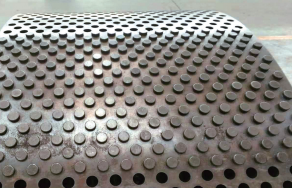
Высококачественная износостойкая поверхность валков со шпильками
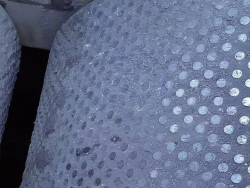
После того, как материалы экструдируются,
на поверхности валка образуется плотный слой материала для защиты поверхности валка.
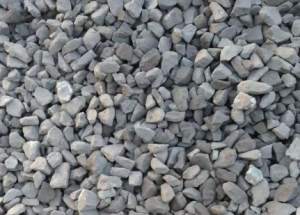
Сырье
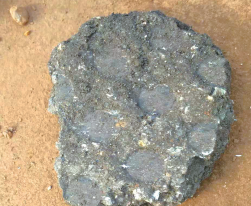
Материал торта